Here’s an overview of emerging processing technologies for metal components, highlighting key innovations and their industrial significance:
1. Additive Manufacturing (AM) of Metal Parts
Powder Bed Fusion (PBF):
Laser-Based (SLM/LPBF): Uses high-power lasers to selectively melt metal powder layers (e.g., titanium, Inconel). Achieves complex geometries (e.g., internal channels, lattice structures) impossible with traditional methods. Post-process heat treatment per GB/T 39247-2020 is critical to relieve residual stress and enhance mechanical properties.
Electron Beam (EBM): Suits reactive metals (e.g., Ti-6Al-4V) in vacuum environments, ideal for aerospace implants.
Binder Jetting: Lowers costs by binding powder with polymers, followed by sintering. Used for stainless steel tooling and automotive parts.
Key Advancements: ISO/ASTM 52904:2024 standardizes PBF processes for critical applications, ensuring performance in porosity control (<0.5%) and fatigue resistance.
2. Hybrid Manufacturing Technologies
Additive-Subtractive Integration: Combines AM with CNC machining. Example: Laser-directed energy deposition (DED) builds near-net shapes, while CNC ensures micron-level tolerances. Reduces material waste by 40% for high-value alloys.
Friction Stir Additive Manufacturing (FSAM): Solid-state process for aluminum alloys. Eliminates melting defects, enhancing tensile strength by 15–20% vs. casting.
3. Advanced Casting & Forming
Rapid Precision Casting (RPC): Integrates selective laser sintering (SLS) of patterns with vacuum differential pressure casting (VDPC). Accelerates prototype-to-production for investment casting of aerospace blades, cutting lead time by 60%.
Microforming: For miniaturized components (e.g., medical devices). Uses laser shock peening to improve formability of thin foils (<100 μm). 4. Digital Process Chains & AI Generative Design + AM: Algorithms optimize topology for weight reduction (e.g., Airbus brackets 30% lighter). In-Process Monitoring: Sensors track thermal gradients during PBF to predict defects. Machine learning adjusts parameters in real-time to minimize spatter and porosity. 5. Surface Engineering Innovations Laser Peening: Induces compressive stress layers to boost fatigue life in turbine blades. Cold Spray Additive Manufacturing (CSAM): Solid-state deposition repairs high-strength components (e.g., military vehicle shafts) without heat distortion. Comparative Analysis of Emerging Processes Technology Key Materials Tolerance (mm) Strength vs. Traditional Primary Applications Laser PBF (SLM) Ti64, AlSi10Mg, 316L ±0.05–0.1 +10–20% Aerospace, medical implants Binder Jetting 17-4PH, Tool steel ±0.2 Comparable to MIM Automotive, tooling Rapid Casting (RPC) Aluminum, Superalloys ±0.3 Matches forging Turbine blades, pumps Cold Spray AM Cu, Al, WC-Co ±0.15 >95% density Repair, coatings
Challenges & Future Outlook
Challenges: High AM equipment costs ($500K–$1M), limited material databases for novel alloys, and post-processing complexity (e.g., HIP, machining).
Trends: Multi-material printing (e.g., Cu-Stainless gradients for heat exchangers), sustainable powders from recycling, and digital twins for lifecycle management.
These technologies redefine metal component manufacturing by prioritizing precision, efficiency, and design freedom—driving advancements from aerospace to biomedical sectors.
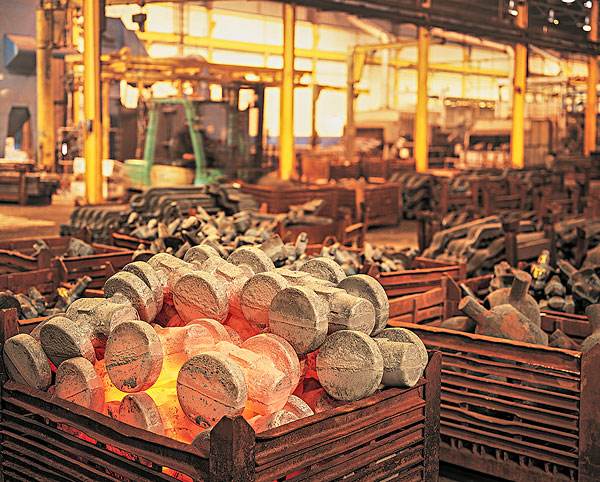