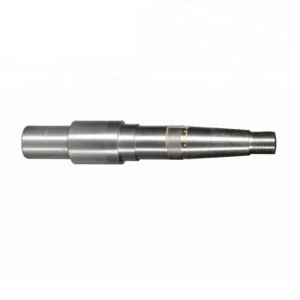
- Requirement Analysis and Process Design
Requirement Analysis: Engage in detailed discussions with the client to clarify the operating environment, performance requirements, dimensional accuracy, surface quality, and other specifications of the metal part.
Process Design: Select the appropriate forging process (free forging, die forging, precision forging, etc.) based on the requirements, and develop a detailed process flowchart. Determine the material, equipment, molds, and other necessary components.
- Raw Material Preparation
Material Selection: Choose the appropriate material (e.g., carbon steel, alloy steel, stainless steel, aluminum alloy) based on the performance requirements of the part.
Material Inspection: Conduct chemical composition analysis, mechanical property testing, and other inspections to ensure the material meets the required standards.
Cutting: Cut the raw material into suitable sizes and shapes according to the process requirements.
- Heating
Heating Equipment: Select the appropriate heating equipment (e.g., box furnace, induction heating furnace) based on the material properties.
Heating Temperature: Heat the metal to the forging temperature range to ensure good plasticity and low deformation resistance.
Temperature Control: Strictly control the heating temperature and duration to prevent defects such as overheating or burning.
- Forging
Free Forging: Use simple tools to plastically deform the metal through manual or mechanical operations, suitable for single-piece or small-batch production.
Die Forging: Place the heated metal into a mold cavity and apply pressure using a press to shape it, suitable for mass production and high-precision parts.
Precision Forging: Utilize more precise molds and processes based on die forging to achieve higher accuracy and more complex shapes.
- Heat Treatment
Annealing: Relieve internal stresses generated during forging, improve organizational uniformity, and enhance machinability.
Normalizing: Refine grain structure, increase strength, and improve toughness.
Quenching: Increase hardness and wear resistance.
Tempering: Reduce brittleness after quenching and improve toughness.
- Machining
Turning: Process external circles, internal holes, end faces, etc.
Milling: Process planes, grooves, gears, etc.
Grinding: Improve surface finish and dimensional accuracy.
Drilling: Create various holes.
- Surface Treatment
Sandblasting: Remove surface oxide layers and burrs to improve surface quality.
Electroplating: Enhance corrosion resistance, wear resistance, and aesthetics.
Coating: Improve rust resistance and appearance.
- Quality Inspection
Dimensional Inspection: Use calipers, micrometers, and other tools to check dimensional accuracy.
Visual Inspection: Inspect surface defects visually.
Non-Destructive Testing: Perform ultrasonic, magnetic particle, or other non-destructive tests to ensure internal quality.
This process ensures that custom forged metal parts meet the highest standards of quality, precision, and performance required by the mechanical industry.